Materials for sensory applications
The sensory properties of electrically conductive composites (CPCs - Conductive Polymer Composites) with carbon-based nanofillers are mainly based on changes in their electrical conductivity when external conditions such as mechanical load (deformation sensing), temperature (temperature sensing) or environmental conditions, e.g. exposure to different media (humidity, liquid and vapour sensing), change. Generally, the change in electrical resistance (Rrel = ΔR/R0) is tracked as a function of the changing condition and/or time and the intensity of the change is inferred from the magnitude and the time course. Good signal recovery and reproducibility are important for this. The quotient between the relative change in resistance and the change in the measurand (e.g. deformation, concentration of a gas or solvent, relative humidity, temperature) is a measure of the sensitivity of the material to the changing influence quantity. For deformation sensors, this quotient is called the gauge factor (GF).
In general, composites with filler contents just above the electrical percolation threshold give the highest signal response, as the associated relatively loose filler networks are disturbed even at small expansion of the matrix and lose their conductivity by increasing the distance between adjacent fillers or breaking contacts. However, the lower signal responses at higher filler contents and denser filler networks generally show better stability and repeatability.
The basic principle of sensory effects is shown schematically below:
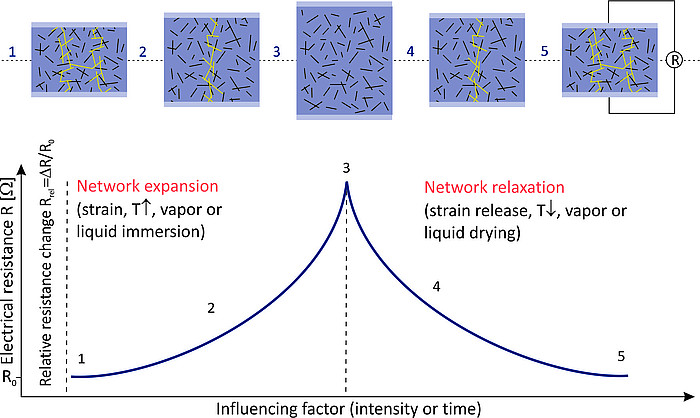
The large variety of possible polymer matrices and conductive fillers enables the development of strain sensors for different strain ranges adapted to the specific requirements. For the detection of deformations and the formation of defects in components (structural health monitoring, SHM), sensors are suitable that give intensive signals even in the case of slight changes in shape. Thermoplastic materials with high resistance to media and suitable strength behaviour were selected for SHM use under harsh conditions.
!["Nuomici" [Ke et al. ACS Appl. Mater. Interfaces 2019, 11, 38, 35362–35370]](/fileadmin/_processed_/csm_Nuomici-Abb_62cb69275f.jpg)
The focus of this work is on CPCs based on polycarbonate (PC) and polyvinylidene fluoride (PVDF). Various concepts for increasing the measurement signal were developed, including the investigation of different CNT functionalisations, the use of mixed filler systems, the addition of ionic liquids or polymer blending, for example with rubber-like polymers or with polymers that are miscible with the basic polymer in the melt. Furthermore, the sensory behaviour of PC fibres spun from the melt was investigated.
Example: Increasing sensitivity (ΔR/R0) by adding CNT-coated acrylic rubber (ACM) to build a hierarchical CNT network, inspired by the Asian speciality "Nuomici" [Ke et al. ACS Appl. Mater. Interfaces 2019, 11, 38, 35362–35370].
For solvent detection in the liquid or vapour state, the work is aimed in the direction of leakage detection, concentration determination and also discrimination of different solvents. The interactions between the analyte molecules and the polymer matrix are decisive for the sensor response. These can be estimated by means of the solubility parameters according to Hansen for polymer and solvent, which enables the prediction of polymer matrices suitable for the solvent to be analysed. Polymer blend materials are of particular interest here, where the two components have different sensitivities to the solvents to be tested and the conductive filler is selectively localised in one of the two components.
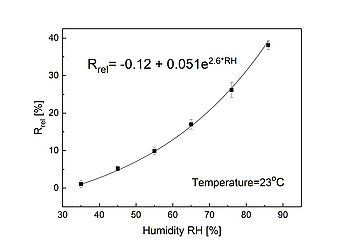
Technical thermoplastics are not suitable for determining humidity due to insufficient interaction with water. Therefore, composites based on cellulose are used for this purpose.
Example (right): Sensitivity (relative resistance change Rrel) of a cellulose film with 5 wt% reduced graphene oxide (rGO) to humidity (RH) [Chen et al. Journal of Materials Chemistry A, 2018, 6, 7777 - 7785].
Aerogels developed from the cellulose composites have a high internal surface area, enabling rapid signal response when sensing water and other hydrophilic gases.
Contact persons
Dr. Petra Pötschke
Dr. Ulrike Staudinger
Dr. Beate Krause
Device for measuring the relative resistance change Rrel at IPF
Flyer