Conventional and reactive mixing
For the preparation of heterophasic elastomer materials the compounding step in specific mixing devices (internal mixer, batch kneader) plays a decisive role. Beside conventional mixing processes for dispersion and distribution of reinforcing and functional (nano)fillers in the rubber matrix also reactive mixing processes are in the focus: Examples are the reactive blending of rubbers and thermoplastics with in-situ cross-linking of the rubber phase by dynamic vulcanization for preparation of Thermoplastic Vulcanizates (TPV) or the in-situ synthesis of PUU in a NBR-rubber matrix, which results in phase-compatibilized elastomer blends with interesting properties. The resulting phase morphology can be influenced and tailored by the process parameters during reactive blending and determines the performance of such elastomers.
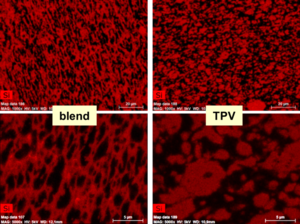
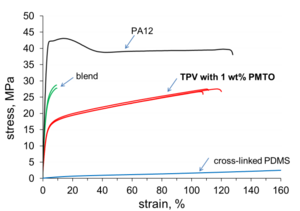
The dispersive and distributive mixing mechanisms are mainly influenced by the flow conditions in the mixer. Their experimental characterization/visualization, supported by fluid flow simulation, helps in getting deeper understanding how the processing parameters affect the morphology development during elastomer mixing.