Methode, Prozessintegrierte Oberflächenmodifzierung beim Spritzgießen
Ablauf am Beispiel der thermoplastischen Formgebung durch Spritzgießen
Schritt 1
Eine dünne Schicht eines reaktiven Polymers (der Modifikator) wird auf die innere Oberfläche der Kavität des Spritzgießwerkzeugs appliziert. Dies kann durch Spray-Coaten, Drucken, Walzen einer Lösung oder durch eine andere Methode erfolgen. Die Beschichtung kann vollflächig oder strukturiert sein. Als Lösungsmittel wird vorzugsweise Wasser verwendet. Technisch kann dieser Schritt nahezu ohne Zeitverlust in die Prozesskette integriert werden, in dem der Applikationsschritt die Zeit des geöffneten Werkzeugs ausnutzen. Die oft höhere Werkzeugtemperatur führt zu einer schnellen Verdampfung des Lösungsmittels. Die dünne Schicht kann auch extern auf einem Substrat erzeugt werden, beispielsweise durch Adsorption, Spin-Coaten oder Drucken. Die Präparation und Charakterisierung dünner Schichten ist eine Voraussetzung zur wissenschaftlichen Bearbeitung. Das Substrat wird dann in das Werkzeug eingelegt.
Schritt 2
Das Werkzeug wird geschlossen, und eine Thermoplastschmelze wird eingespritzt. Durch die hohe Temperatur der Schmelze kommt es zu einer Reaktion, die den Modifikator chemisch fest an die spätere Formteiloberfläche bindet.
Schritt 3
Beim Entformen wird die Modifkatorschicht vom Werkzeug auf die Formteiloberfläche übertragen.
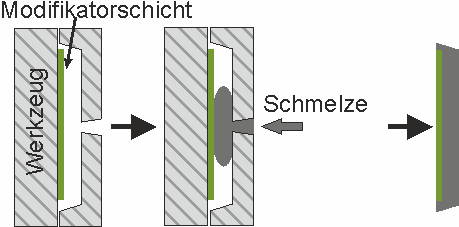
Besonderheiten
- Energieeffizient: Ausnutzung des Energieaufwands des Schmelzens des Thermoplasts zur Initiierung chemischer Reaktionen
- Gezielte Modifizierung: Die Ausrüstung der Oberfläche mit funktionellen Gruppen wird über die Struktur des Modifikators gesteuert.
- Hohe Effektivität durch Prozessintegration: Die Oberflächen zum Lackieren oder Verkleben müssen nicht in einem separaten Schritt vorbehandelt werden.
- Hoher Modifizierungseffekt: Der Modifikator weist hohe Dichte funktioneller Gruppen auf, die die chemischen Eigenschaften der Formteiloberfläche prägen.
- Alle Vorteile des Sprtzgießprozesses bleiben erhalten:
- Hohe Produktivität
- Reproduzierbarkeit
- Hohe Oberflächenqualität
Forschungsarbeiten: Analyse der prozessbedingten Vorgänge
Die Schmelze ist eine viskose Flüssigkeit. Dadurch erfolgt die Schmelzeströmung auch bei hohen Einspritzgeschwindigkeiten laminar. Typischerweise tritt eine Haftung der Schmelze an der Werkzeugwandung auf. Daraus resultiert eine Quellströmung: Die Geschwindigkeit ist in der Mitte des Querschnitts am größten. Hier wird immer heiße Schmelze nachgeliefert.
Unter Aufweitung des Querschnitts durch nachströmende Schmelze wird die Werkzeugoberfläche durch die Schmelze kontaktiert. Die Kraft wirkt nahezu senkrecht zur Werkzeugoberfläche. Es findet keine Durchmischung von Modifikator und Schmelze statt. Dies ist die Grundlage, um feine Strukturen chemischer Modifizierungen auf dem Formteil zu realisieren. Unsere Arbeiten befassen sich mit den Wechselwirkungsmechanismen für Strukturierungen im Mikro- bis Nanometerbereich.
Bei Kontakt der Schmelze mit dem Werkzeug kühlt diese schlagartig ab und erstarrt. Die Zeit, in der eine hohe Temperatur für die Initiierung von chemischen Reaktionen, für Diffusionen von Molekülen oder Polymersegmenten oder für Benetzungen in kleinen Strukturen, ist sehr kurz. Unter typischen Verarbeitungsbedingungen liegt beispielsweise bei PC eine ausreichend hohe Temperatur nur für eine Zeit in der Größenordnung von 1 µs vor [lit]. In dieser Zeit legt die Schmelze typischerweise einen Weg von ca. 100 nm zurück. Die Reaktion beginnt also beim Kontakt der Schmelze mit dem Modifikator an der Werkzeugoberfläche und endet typischerweise nachdem die Schmelze einen Weg von 100 nm zurückgelegt hat. Beim Einspritzen ensteht also eine Reaktionsfront, die sich mit der Schmelzeströmung bewegt.
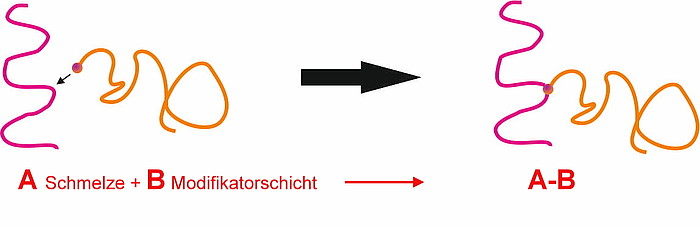
Ein Schwerpunkt der Arbeiten besteht in der Identifizierung geeigneter schneller Reaktionen für unterschiedliche Thermoplaste.
Die Kontaktierung der Reaktionspartner kann nur durch Interdiffusion erfolgen. Das trifft für alle Arten der Verbundbildung durch Zweikomponentenspritzgießen, Heißpressen, Schweißen, Kleben zu. Der Interdiffussionsschichtdicke kommt eine große Bedeutung zu. Sie ist für Paarungen mischbarer Polymere beliebig groß und wird nur durch die Zeit begrenzt. Die Diffusionsgeschwindigkeit hängt dabei von der Temperatur ab, speziell von der Temperaturdifferenz bis zur Glasübergangstemperatur. In fast allen Fällen sind Polymerpaare jedoch unmischbar. Dies trifft vor allem zu bei chemisch unterschiedlichen Polymeren. Im Fall des oberflächenreaktiven Spritzgießens sind Modifikator und Thermoplast geradezu konträr, da ja durch chemische Oberflächenmodifizierung eine grundlegende Änderung der chemischen und physikalischen Eigenschaften erreicht werden soll. Für diesen Fäll hängt die Interdiffusionsschichtdicke nach Helfand vom Flory-Huggins-Parameter ab:
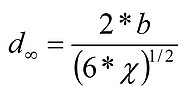
mit b = Länge der statistischen Segmente, χ = Flory-Huggins-Parameter und d∞ = Interdiffusionsschichtdicke im Gleichgewicht. Bei typischen Polymerpaarungen liegt sie in der Größenordnung von bis zu 10 nm, nach unendlicher Zeit. Dies trifft für alle Verbundbildungen (s. oben) aus unterschiedlichen Polymeren zu. Die Dicke ist natürlich für die beim Spritzgießen typischerweise auftretenden Temperaturen und kurzen Zeiten noch kleiner. Nach jetzigem Stand der Forschung liegt sie bei wenigen Nanometern. Das entspricht bei vielen Polymeren ungefähr der Länge des statistischen Segments. Daraus ergibt sich ein sehr beengter Reaktionsraum. Charakteristisch für den Diffusionsprozess ist daher die Bewegung des Monomers innerhalb des Segments. Auf der anderen Seite muss die chemische Umsetzung innerhalb dieses Reaktionsraumes schnell verlaufen und eine ausreichende Ausbeute liefern. Beobachtungen mit praktischen Systemen ergaben eine Bevorzugung von einfachen Kopplungs- und Einspaltungsreaktionen der Monomersegmente A und B, wie A + B → … . Komplexe Reaktionsketten, die auf einer Reihe von Folgereaktionen basieren, verliefen oft nur unvollständig. In Ergänzung zur analytischen Untersuchung, die unter diesen Bedingungen nur schwer realisierbar ist, dienen Computersimulationen. Mit Hilfe von groben Polymermodellen wurden Systeme untersucht, die den typischen Größen und Zeiten nahe kommen. Einfache End-zu-End-Verknüpfungen waren relativ langsam. Erwartungsgemäß verliefen Reaktionen mit Polymeren, die eine hohe lokale Konzentration an reaktiven Gruppen tragen, am schnellsten. Darüber hinaus entstanden in bestimmten Fällen Riesenmoleküle. Deren Einfluss auf die Verbundbildung ist noch nicht ganz klar. Allgemein wird daher geschlussfolgert, dass Reaktionen von Polymeren unter den besonderen Bedingungen am effektivsten verlaufen, wenn die Glasübergangstemperatur niedrig, die lokale Konzentration reaktiver Gruppen hoch und die Reaktion aus möglichst wenigen Schritten besteht. Das deutet darauf hin, die Diffusion der Reaktionspartner, die hier durch die hohe Temperatur unterstützt wird, der geschwindigkeitsbestimmende Schritt und die Reaktivität der Reaktionspartner hoch genug ist. Tatsächlich gelang es für eine Reihe von Thermoplasten wie Polycarbonat, geeignete Modifikatoren und Bedingungen zu finden, die eine effektive Oberflächenmodifizierung bewirken.
Projekte
auf den Gebieten, nach Projektträger
DFG
„Neue Wege zur Oberflächenaktivierung von Kunststoffen“, DFG-Forschergruppe zusammen mit Lehrstuhl für Kunststofftechnik der TU Chemnitz, 1998-2002
„Chemische Oberflächenmodifizierung beim Spritzgießen und dessen Wechselwirkung mit dem Verarbeitungsverhalten“, Verbundprojekt mit Lehrstuhl für Kunststofftechnik der TU Chemnitz , 2003-2005
„Modellierung und Simulation von Reaktionen an Grenzflächen von Polymerschmelzen zur Verbundbildung“, 2007-2009
„Immobilisierung von Nanoteilchen auf Kunststoffoberflächen mit Hilfe funktioneller Polymere durch oberflächenreaktives Spritzgießen“, 2011-2012
AiF
„Methode zur chemischen Oberflächenmodifizierung von Polyolefinen bei der Formgebung“, 2003-2005, Verbundprojekt mit FILK Freiberg und Lehrstuhl für Kunststofftechnik der TU Chemnitz
„Kunststoffformteile mit permanent elektrisch ableitfähiger Oberflächenschicht (Ableitfähige Kunststoffe)“, Verbundprojekt mit IOT der HS Zittau
Volkswagen-Stiftung
„Fast Surface Reactions on Moulding“ , Verbundprojekt mit Lehrstuhl für Kunststofftechnik der TU Chemnitz, 2007-2010
„New Surface Functionalisation by Process-Integrated Surface Modification of Polyolefins“ , Verbundprojekt mit Lehrstuhl für Kunststofftechnik der TU Chemnitz, 2010-2012
Veröffentlichungen in Zeitschriften zu den Themen
- J. Nagel, M. Bräuer, B. Hupfer, K. Grundke, S. Schwarz, D. Lehmann, „Investigations on the reactive surface modification of polycarbonate by surface-reactive injection molding“, J. Appl. Polym. Sci, 93 (2004) 1186-1191
- R. Brunotte, H. Kolz, J. Nagel, „Vorbereitung zum Lackieren und Kleben: Inline-Oberflächenmodifizierung im Spritzgießprozeß“, Kunststoffe (2005) 67-70, und Kunststoffe plast europe (2005) H. 01
- X. He, J. Nagel, D. Lehmann, G. Heinrich, „Interface Structure between Immiscible Reactive Polymers under Transreaction: a Monte Carlo Simulation“, Macromol. Theory Simul. 14 (2005) 305–311
- R. Brunotte, G. Mennig, J. Nagel, „In-situ Surface Modification of Polycarbonate During Injection Moulding“,Journal of Plastics Technology / Kunststofftechnik, (2006) 4, 1-7
- J. Nagel, R. Brunotte, B. Hupfer, K. Grundke, D. Lehmann, G. Mennig, „Investigations into the chemical modification of polyolefin by radical reactions during molding“, Macromolecular Reaction Engineering 1 (2007) 480-487
- A. John, J. Nagel, G. Heinrich, „Monte Carlo simulation of polymer reactions at interfaces“, Macromolecular Theory and Simulations 16 (2007) 430-440
- Th. Härtig, J. Nagel, M. Gehde, D. Lehmann, G. Heinrich, “Prozeßintegrierte Oberflächenmodifizierung beim Spritzgießen”, Kunststoffe 2010, 1, 38-42; “Process-integrated surface modification during injection molding, Kunststoffe International, 2010, 1, 31-35
- Andreas John, Jürgen Nagel, Gert Heinrich, „Compatibilization in Two-Component Injection Molding by Means of Split Reactions with Varying Reactive Sites – a Monte-Carlo Simulation“, The Open Macromolecules Journal, 2011, 5, 1-12 1
- Jürgen Nagel, Petchara Chunsod, Cordelia Zimmerer, Frank Simon, Andreas Janke, Gert Heinrich, „Immobilization of Gold Nanoparticles on a Polycarbonate Surface Layer During Molding“, Mater. Chem. Phys. 129 (2011) 599– 604
- Andreas John, Jürgen Nagel and Gert Heinrich, „Monte-Carlo Simulation of Compatibilization by Network-Building and Catalytic Interface Reactions in Two-Component Injection Molding“, The Open Macromolecules Journal, Volume 6, 2012, 1-18
- J. Nagel, G. Heinrich, Temperature transitions on the surface of a thermoplastic melt during injection moulding and its use for chemical reactions, International Journal of Heat and Mass Transfer 55 (2012) 6890–6896
- Rene Brunotte, Jürgen Nagel, Günter Mennig, Gert Heinrich, Michael Gehde, Polyolefin Surface Modification During Injection Molding Using Radical Reactions in Liquid Phase, Macromol. React. Eng. 8 (2014) 412–417
- Jürgen Nagel, Felix-Aron Pahner, Cordelia Zimmerer, Thomas Härtig, Michael Gehde, Gert Heinrich, Electrostatic Discharging Behaviour of Polycarbonate Parts Made by Process-Integrated Surface Modification, Macromol. Mater. Eng. 2014, 299, 1395–1402